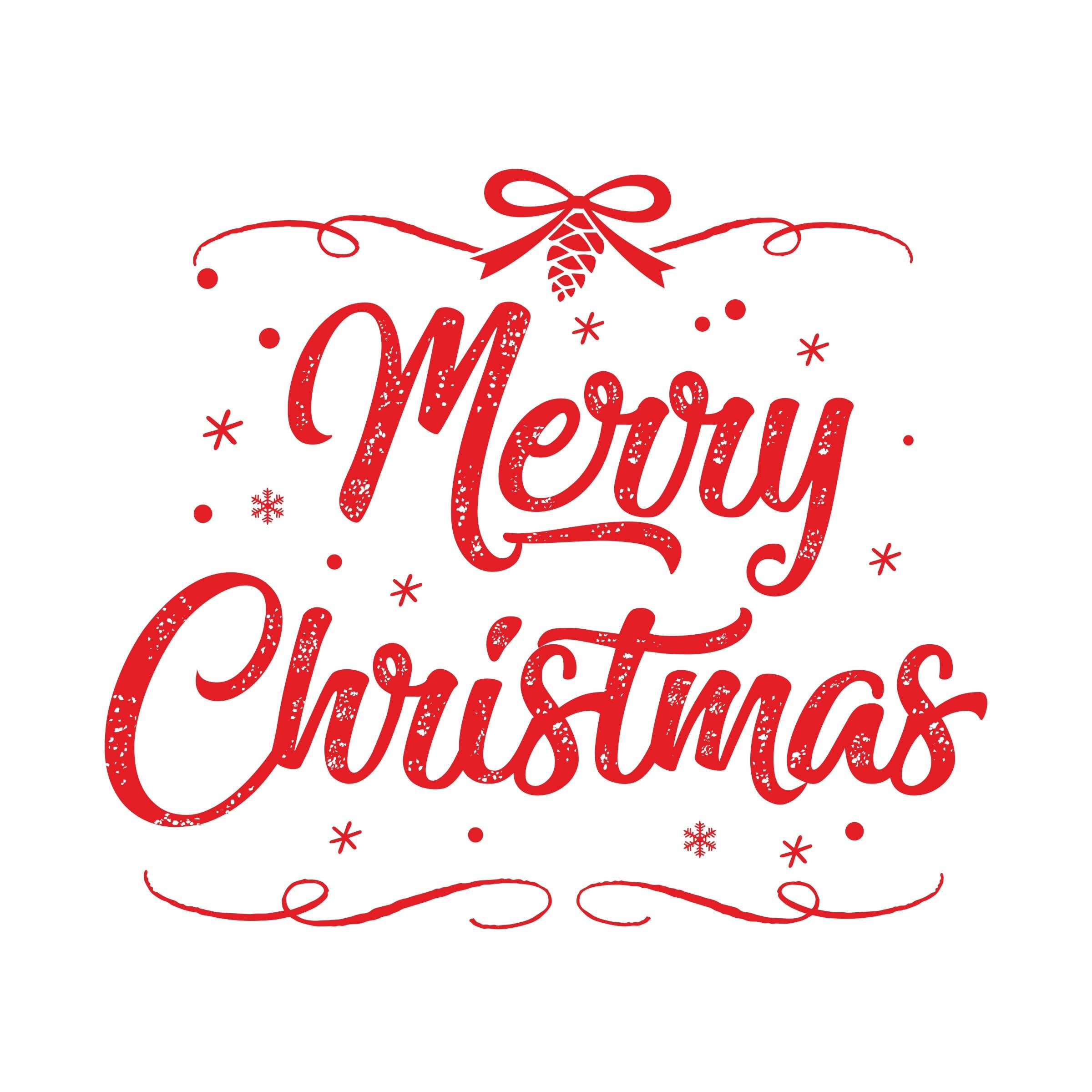
Keeping it Clean: The Vital Role of Sanitary Valves in Chemical Plants
Chemical plants are complex environments, handling a vast array of substances, many of which are highly corrosive, reactive, or require strict purity standards. Maintaining hygiene and preventing contamination is paramount, not just for product quality but also for safety and regulatory compliance. This is where sanitary valves play a crucial, yet often overlooked, role.
Unlike standard industrial valves, sanitary valves are specifically designed to minimize crevices, dead spaces, and other areas where bacteria, product residues, or contaminants can accumulate. This makes them essential for processes involving sensitive chemicals, pharmaceuticals, food processing within chemical plants (like additives or preservatives), and other applications where hygiene is critical.
What sets Sanitary Valves apart?
Several key features distinguish sanitary valves from their industrial counterparts:
Smooth Internal Surfaces: Sanitary valves are manufactured with highly polished internal surfaces, often using electropolishing techniques. This minimizes surface roughness, preventing product buildup and facilitating efficient cleaning.
Crevice-Free Design: The design minimizes or eliminates areas where product can become trapped. This includes features like flush connections, minimal dead legs, and smooth transitions between components.
Materials of Construction: Typically constructed from corrosion-resistant materials like 316L stainless steel, sanitary valves can withstand harsh chemical environments and frequent cleaning.
Easy Cleaning and Sterilization: Sanitary valves are designed for Clean-in-Place (CIP) and Sterilize-in-Place (SIP) procedures. This allows for efficient cleaning and sterilization without dismantling the valve, reducing downtime and labor costs.
Specific Connection Types: Sanitary connections like Tri-Clamp (Tri-Clover) or aseptic flanges are commonly used. These connections are designed for quick disassembly, easy cleaning, and leak-free performance.
Types of Sanitary Valves Used in Chemical Plants:
Several types of sanitary valves find application in chemical processing:
Sanitary Ball Valves: These valves provide reliable on/off control with minimal pressure drop. Their smooth internal bore makes them suitable for viscous fluids and minimizes product entrapment.
Sanitary Butterfly Valves: Offering efficient flow control and quick actuation, butterfly valves are often used in larger diameter lines. Sanitary versions feature smooth discs and hygienic seals.
Sanitary Diaphragm Valves: Ideal for handling highly viscous or abrasive fluids, diaphragm valves isolate the process fluid from the valve mechanism, preventing contamination and simplifying cleaning.
Sanitary Check Valves: These valves prevent backflow, ensuring unidirectional flow in the process line. Sanitary designs minimize crevices and facilitate cleaning.
Applications in Chemical Plants:
Sanitary valves are crucial in various chemical plant applications, including:
Pharmaceutical Production: Manufacturing of active pharmaceutical ingredients (APIs) and other pharmaceutical products requires stringent hygiene standards, making sanitary valves essential.
Food Additive and Preservative Manufacturing: Chemical plants producing food-related products must adhere to food safety regulations, necessitating the use of sanitary valves.
Specialty Chemical Production: Processes involving sensitive or high-purity chemicals benefit from the hygienic design of sanitary valves.
Water Treatment and Purification: Sanitary valves are used in water treatment systems within chemical plants to ensure the quality of process water.
Conclusion:
While often unseen, sanitary valves play a critical role in maintaining product quality, ensuring safety, and meeting regulatory requirements in chemical plants. Their unique design features and materials of construction make them indispensable for processes demanding high levels of hygiene and contamination control. Choosing the right type of sanitary valve for a specific application is crucial for optimal performance, efficiency, and long-term reliability. By prioritizing hygienic design and proper valve selection, chemical plants can ensure smooth, safe, and compliant operations.