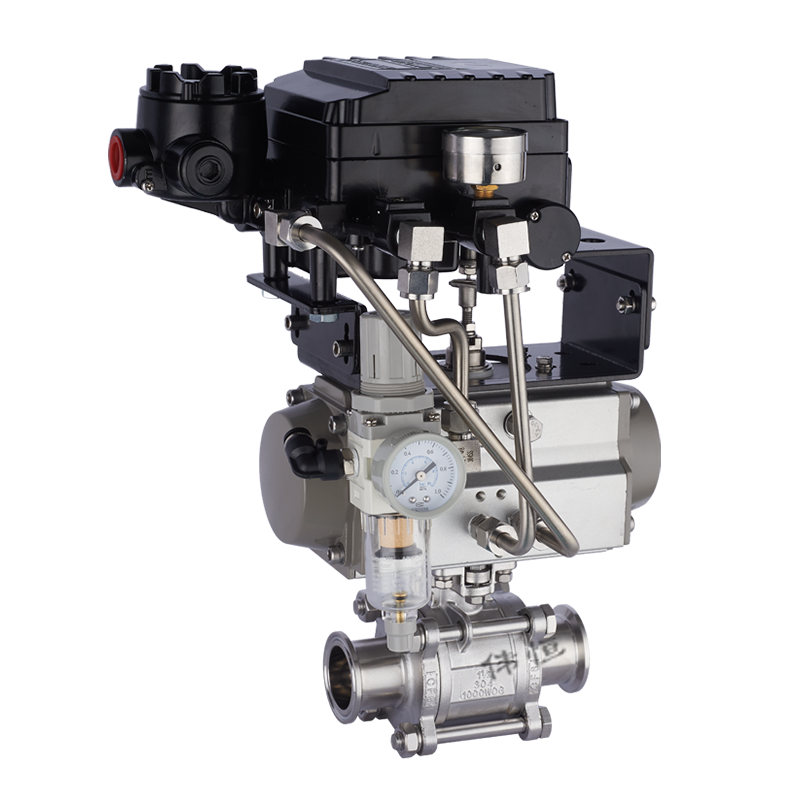
Sanitary ball valves are widely used in industries with extremely high hygiene requirements such as food and pharmaceuticals. When using them, you need to pay attention to several key points to ensure their performance and hygiene standards:
1. Installation precautions
Cleaning pipes and valves: Before installing sanitary ball valves, be sure to thoroughly clean the pipes and valves to remove impurities, dirt, rust, etc. in the pipes to prevent these contaminants from entering the valves and affecting the sealing performance of the valves and the rotation flexibility of the ball, while avoiding contamination of the medium flowing through. The valve itself must also ensure that there are no impurities left, especially the inner surface in contact with the medium, which should meet the corresponding hygiene and cleaning standards.
Correct installation position: Choose a suitable installation position according to the process flow and operation requirements. Generally, the valve should be installed in a place that is easy to operate and maintain, and avoid installing it in inaccessible corners or narrow spaces. At the same time, the direction and support of the pipeline should be considered to ensure that the valve will not be subjected to additional forces due to the stress of the pipeline after installation, affecting its normal operation.
Connection method specifications: Common connection methods for sanitary ball valves include clamp connection, welding, threaded connection, etc. When using clamp connection, ensure that the specifications of the clamp match the valve and pipeline, and tighten the clamp bolts evenly during installation to ensure the sealing effect; welding connections must be operated by professional welders in accordance with welding process specifications, control welding parameters, prevent welding deformation from affecting valve performance, and perform flaw detection and cleaning on the welds after welding; threaded connections must pay attention to the thread matching accuracy, apply an appropriate amount of sealant to avoid leakage.
2. Key points for operation and use
Control the opening and closing force: When operating a sanitary ball valve, whether manually or through an actuator, the opening and closing force must be controlled. Avoid excessive force that may damage the valve stem, ball or seal. When operating manually, turn the handle smoothly. If you feel obvious resistance, do not force the operation. Check whether the valve is faulty or stuck with foreign objects. For valves controlled by pneumatic or electric actuators, ensure that the air source pressure or power supply voltage of the actuator is stable within the specified range to prevent abnormal valve movement due to abnormal power.
Avoid frequent opening and closing: During normal operation, the frequent opening and closing of sanitary ball valves should be minimized. Frequent opening and closing will accelerate the wear of the seals and reduce the service life of the valve. It may also cause the sealing performance to deteriorate and leakage to occur. Only when it is necessary to adjust the flow or cut off the medium, the necessary valve operation is performed.
Avoid overpressure operation: strictly control the pressure of the medium in the pipeline so that it can operate within the rated working pressure range of the sanitary ball valve. Overpressure operation may cause serious consequences such as valve seal failure and valve body rupture. Appropriate pressure monitoring devices and safety valves should be installed in the pipeline system. When the pressure exceeds the set value, the safety valve automatically opens to release the pressure to protect the valve and the entire pipeline system.
3. Maintenance requirements
Regular cleaning: Clean the sanitary ball valve regularly, especially the part in contact with the medium. Cleaners that meet hygienic requirements and soft cleaning tools, such as soft cloths and sponges, can be used to remove dirt and sediment on the surface and inside of the valve. For parts that are difficult to clean, appropriate cleaning equipment, such as high-pressure water guns, can be used (but pay attention to pressure control to avoid damage to the valve). Rinse with clean water after cleaning and ensure that there is no detergent residue inside the valve.
Check the seals: Check the seals of the valve regularly, including the seat seals and ball seals. Observe whether the seals show signs of wear, aging, deformation or damage. If there are any problems with the seals, they should be replaced in time to ensure the sealing performance of the valve. The replacement cycle of the seals can be determined according to factors such as the frequency of use of the valve, the characteristics of the medium and the working environment. It is generally recommended to carry out preventive replacement after a certain period of use or number of operations.
Lubrication and maintenance: Regularly lubricate the moving parts of the valve, such as the valve stem and the rotating parts of the ball. Select lubricants that meet the hygiene standards, apply or inject an appropriate amount of lubricants to reduce friction between parts and ensure that the valve operates flexibly and smoothly. The frequency of lubrication should also be determined according to the actual use. Generally, lubrication and maintenance can be carried out at the same time when cleaning the valve.
Performance test: Regularly perform performance tests on sanitary ball valves, such as sealing tests, opening and closing flexibility tests, etc. Professional testing equipment and methods can be used to simulate actual working conditions to test the valve. Through performance testing, potential problems with the valve can be discovered in time, and corresponding maintenance or replacement measures can be taken to ensure that the valve is always in good working condition.